ROBO Carry Rack
For More Information, Click Here
In warehouse storage, increasing the capacity is the most important factor.
Even in the narrow spaces within warehouses. high-density storage with flexible rack arrangements can significantly increase the capacity.
In addition, costs are reduced by automating the transportation between processes and peripheral work before and after storage.
Even in the narrow spaces within warehouses. high-density storage with flexible rack arrangements can significantly increase the capacity.
In addition, costs are reduced by automating the transportation between processes and peripheral work before and after storage.
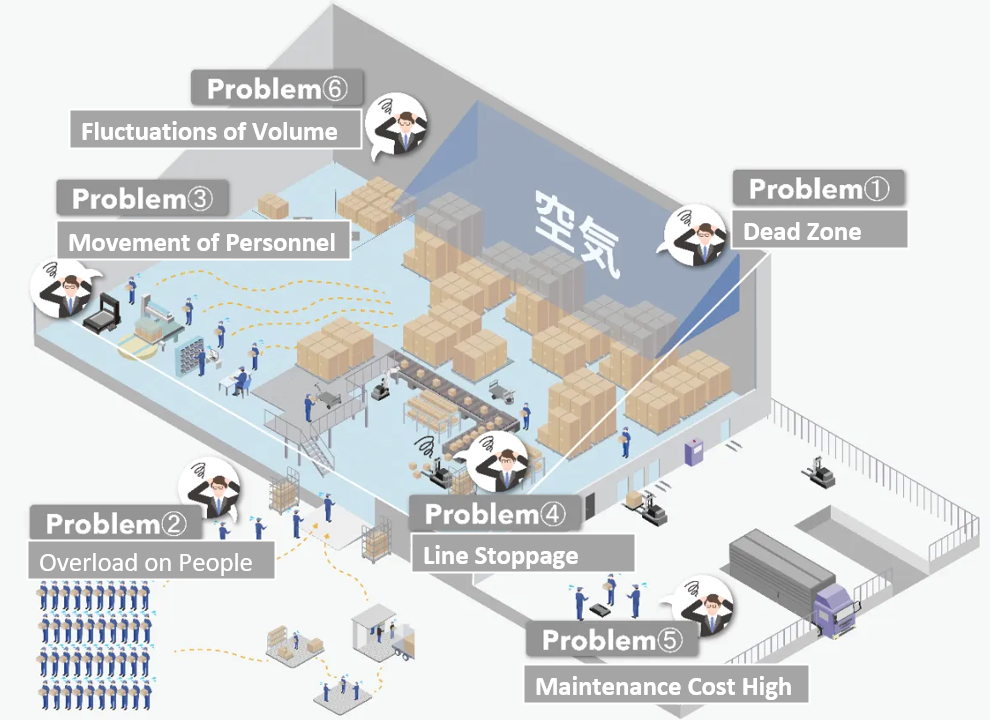
Do you having any of these problems?
Problem 1 : Dead zones occur and space cannot be used effectively.
Problem 2 : Heavy burden on people, leading to lower retention rates and a labor shortage.
Problem 3: A lot of Tasks that heavily depend on manpower.
Problem 4: There are many types of material handling equipment in the warehouse system, and if any one of them breaks down will lead to entire line will stop.
Problem 5:Increase Maintanance cost
Problem 6: Uncertain of seasonal fluctuations in volume and future increases in volume
Leave it to NKC's Automated Storage & Retrieval System (AS/RS)!
High-density storage even in tight spaces is possible!
System that automates everything from storage to peripheral tasks, we achieve both "improved productivity" and "ease of work" for people.
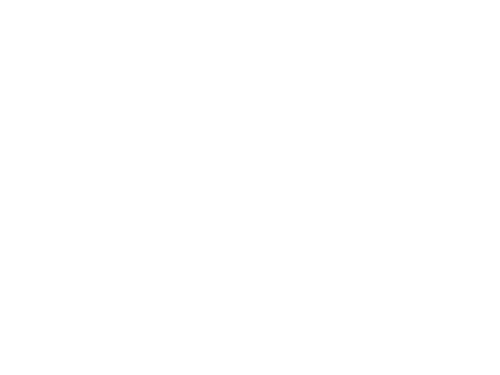
ROBO Carry Rack
1.Effective use of space with flexible rack layouts and manoeuvrable AGVs
Each layer can be combined with a different rack layout and rack height, minimizing wasted space and enabling storage according to your desired operation.
AGVs can move forward and backward, sideways, and spin turns, allowing for space-saving manoeuvring even in limited layouts.
2.The only AGV that can move both inside and outside the rack, reducing the burden on workers
NKC is the only AGV that can move both inside and outside the rack.
Since the goods are transported automatically to the workers who pick and put them in the rack, there is no need for people to move. Not only does it reduce the physical burden on workers, it also improves productivity and allows the use of conventional movement paths as storage space, which directly translates to sales.
3.Automation other than storage and removal reduces the labour required for the entire warehouse.
Automation of tasks surrounding the automated warehouse, such as baggage transport, wrapping, labelling, weight measurement, reloading, and transporting empty pallets, is also possible. If there are no transport instructions, the robot will return to its home position and automatically charge, resulting in significant labour savings.
4.Material handling equipment is consolidated into one type of AGV. Even if an error occurs in one unit, other AGVs can be substituted to prevent line stoppage.
Even if an error occurs in one AGV, other AGVs can be substituted, so the risk of line stoppage and work delays is greatly reduced. Errors can be resolved while the line is running.
5.By consolidating the functions of various devices into one model, maintenance costs are significantly reduced. Maintenance can also be performed in a safe location.
One AGV can now handle the functions of multiple devices that were previously required, reducing the number of spare parts and maintenance required to just one model. Since the AGV automatically drives to the maintenance area on the ground, there is no need for people to work at high altitudes, ensuring safety.
6.By increasing the number of AGVs and adding shelves, we can flexibly respond to changes in material volume.
Even if the volume of goods changes, no major facility construction is required; the volume can be flexibly increased by simply increasing the number of AGVs or adding shelves.
Specification Details
Maximum payload | 500kg | 1000kg |
Speed | Floor travel: 60m/min Rack Travel: 60m/min |
Floor travel: 35m/min Rack Travel: 50m/min |
Deadweight | 400kg | |
Moving Function | Forward, backward, sideways, spin turn | |
Minimum turning radius | 800mm (travel speed 15m/min~30m/min) | |
Stopping Accuracy | ±10mm | |
Navigation | Magnetic tape, magnetic bar, QR code | |
Communication features | Wireless communication, Bluetooth communication | |
Charging function | Automatic charging | |
Battery Type | Lithium-ion battery | |
Lift Mechanism | Lifting height: 42mm | |
Working environment | Temperature: 0 to 40°C (but do not freeze) | |
Humidity: 35~85RH (but no condensation) | ||
Safety devices | Emergency stop button | |
Obstacle Sensor | ||
Bumper Sensor |
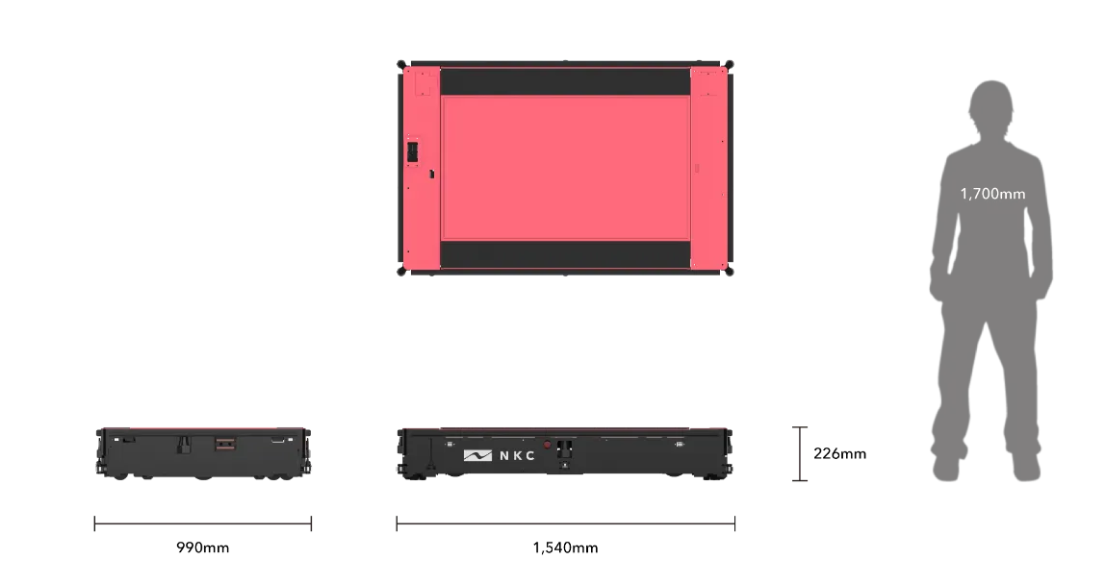
Contact us
DROP US A MESSAGE