ROBO Rook
For More Information, Click Here
Until now, AGVs had various restrictions on where to lay the unmanned transportation route.
NKC's AGV combines three control methods, ``magnetic tape,'' ``SLAM,'' and ``QR code,'' allowing it to continue running in places where unmanned transportation was difficult until now, and realizing production line automation and efficiency.
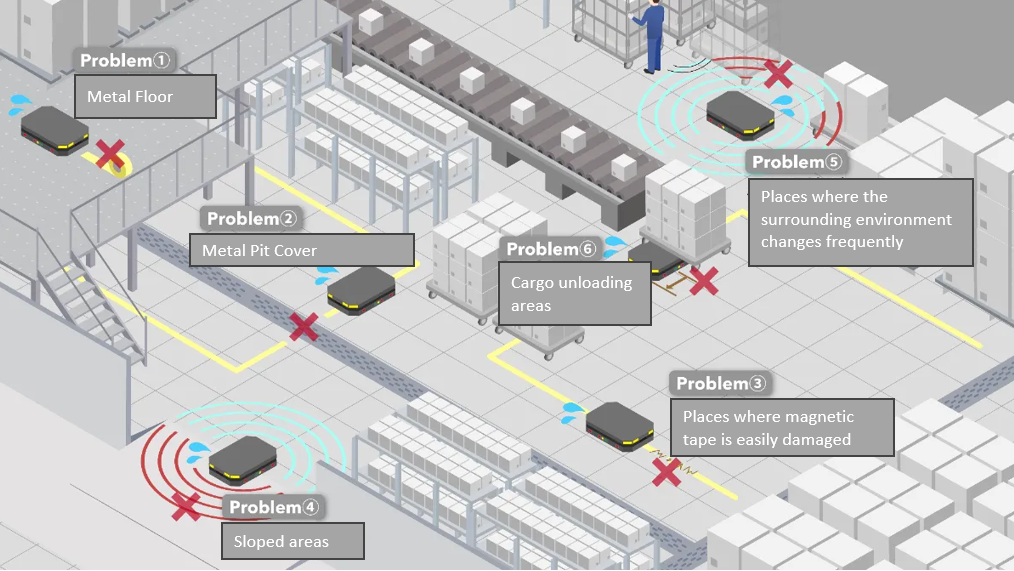
Do you having any of these problems?
Problem ①Metal floor
Magnetic tape cannot be used on magnetic metal floors such as mezzanine racks, and unmanned transport routes cannot be installed.
Problem ②metal pit cover
Magnetic tape cannot be used on magnetic metal pit covers, so the route must be set to avoid pit covers.
Problem ③: Places where magnetic tape is easily damaged
In areas where heavy objects such as forklifts pass, magnetic tape is easily worn and damaged, requiring frequent replacement.
Problem ④: Slope Area
There is a limit to the permissible slope that SLAM can detect, so autonomous driving with SLAM is not possible on sloped locations.
Problem ⑤:A place where the surrounding environment often changes
SLAM will not be able to correctly recognize its own position if the environment changes after mapping, such as when surrounding obstacles move, making autonomous driving difficult.
Problem ⑥: Loading and unloading area
Stopping accuracy of 10 to 15 mm is required to fit perfectly under a cart loaded with cargo.
Toughness with a load capacity of 1 ton and the strongest running performance.
Easily install unmanned transportation tracks within your factory.
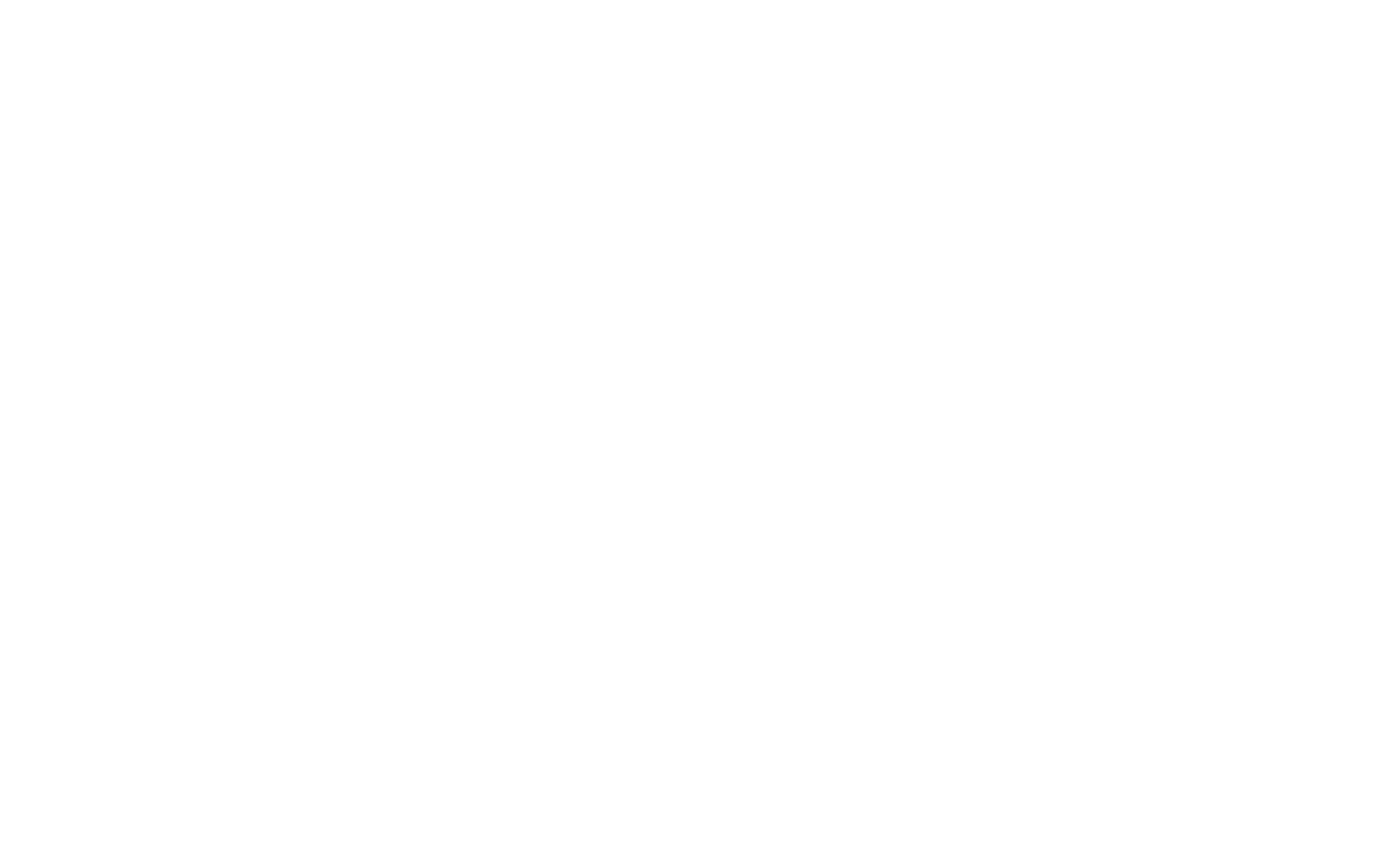
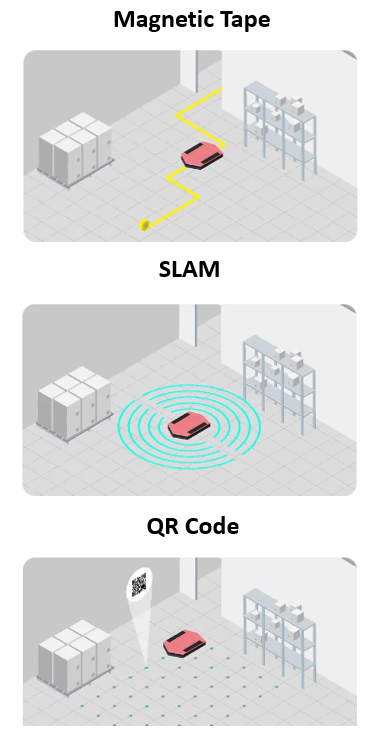
Navigation Method:
Magnetic Tape
You can set a running route by simply pasting magnetic tape on a non-magnetic floor surface. Sensors on the aircraft detect the magnetic field from the tape and control the travel route.
SLAM
SLAM is a control method that uses sensors such as cameras and lasers, encoders, and gyroscopes to estimate self-position and create an environment map.
QR Code
By installing QR codes at stopping points and intersections when using SLAM, and at speed change points when using magnetic tape, it is possible to confirm the exact location and enable more accurate control.
ROBO Rook
Problem ①Metal floor
On the metal floor mezzanine, the robot estimates its position using SLAM and accurately recognizes stopping points and intersections using QR codes. It can travel autonomously even on mezzanine floors where people cannot ride, making effective use of the upper floors of a factory
Problem ②metal pit cover
By switching to SLAM control using the QR code as a marker, you can set a driving route without having to worry about metal parts such as pit covers. This allows for efficient transport of cargo without unnecessary detours.
Problem ③: Places where magnetic tape is easily damaged
SLAM is used in locations where magnetic tapes are easily damaged by dirt, wear, or breakage, eliminating the need to replace damaged tapes.
Problem ④: Slope Area
Since magnetic tape can be used on sloped areas, it can be installed on the water slope at the entrance to a factory. When combined with a QR code, speed adjustment and operation switching can be done accurately.
Problem ⑤:A place where the surrounding environment often changes
Since magnetic tape has a fixed track, it is not affected by changes in the surrounding environment and can run stably.
Problem ⑥: Loading and unloading area
The magnetic tape allows for highly precise control, so it can slip under any type of trolley with precision. When used in conjunction with a QR code, it can switch to a slower speed from a specified position and travel through narrow spaces.
Specification Details
Model | NK-L-AGV500-001 | NK-L-AGV1000-001 |
Deadweight | 260kg | |
Maximum load capacity | 500kg | 1,000kg |
Size | 1,350mm x 850mm x 180mm (height) | |
Moving functions | forward, reverse, turning, curve | |
Traveling speed | 60m/min | 30m/min |
Minimum turning radius | 1,500mm | |
Stopping accuracy | Magnetic: ±10mm SLAM: ±25mm | |
Allowable step/slope | 2mm/0.6° | |
Navigation | Magnetic induction, SLAM, QR code | |
Drive system | Two-wheel speed differential steering system | |
Communication function | Wi-Fi (compliant with 4 standards: IEEE802.11n/a(W52/W53/W56*1)/b/g) (During manual operation: Bluetooth® 4.0+EDR/LR compatible) | |
Charging function | Automatic charging method | |
Battery capacity | 35AH | |
Voltage | 26.4V | |
Charging time | Approximately 30 minutes | |
Running time | Approximately 4 hours (when transporting 1,000kg) | |
Lifespan | More than 14,000 times 100%DOD | |
Lift mechanism | Lifting height: 40mm | |
Environment | Temperature: 0 to 40℃ (but not freezing) | |
Humidity: 20-80% (no condensation) | ||
Safety equipment: | Obstacle sensor | |
Contact stop bumper switch | ||
Melody ringing | ||
Indication by blinker |
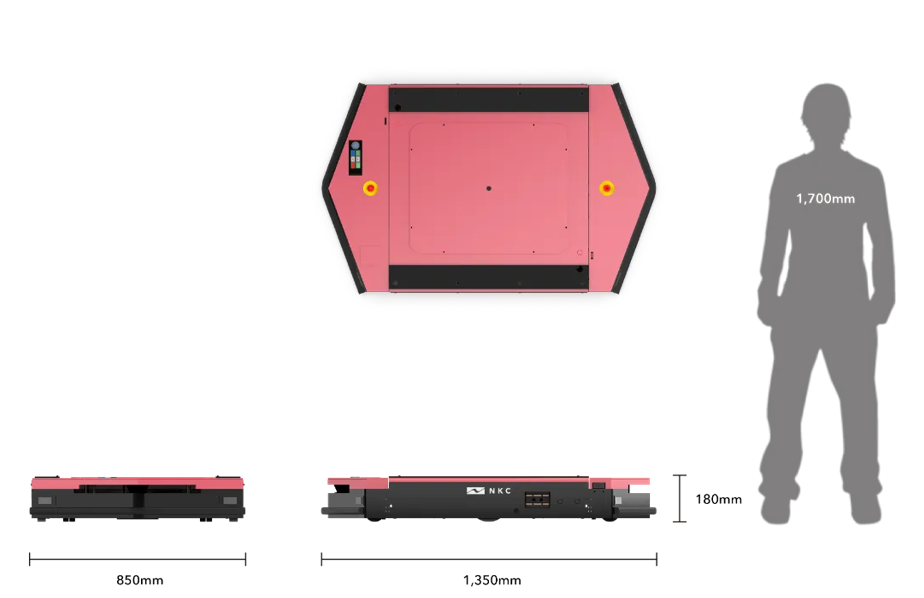
Contact us
DROP US A MESSAGE